RISK
MANAGEMENT:
RISK
MANAGEMENT
Construction projects are
inherently risky. RSG knows that each project will have risks
associated with safety, cost, quality, schedule, environmental
compliance, and operations. Our approach to construction risk
management is to plan and prepare contingency plans. Each Risk
Management Plan will include a description of each probable risk,
probability of occurrence, mitigation measures, an action plan for each
mitigation measure, the methodology to measure the effectiveness of
each measure, and the frequency of review and updating. The status of
each Risk Management Plan will be included in the Project Construction
Manager’s monthly project status report to the Client’s
representative.
Our detailed perspectives of discernible risks that are required to
ensure the success of the project are as follows:
- Public Safety
- Environmental Safety
- Owner Cost
- Schedule Impacts
- Material and Installation Defects
- Worker Safety
- Public Access & Convenience
As the CM, the RSG Team as a whole must examine each task and determine
the possible risks in each of these areas and work with the
Client’s staff and the Contractor to eliminate or reduce the
discernible risk in each area.
|
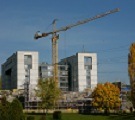
|
CONSTRUCTION
INSPECTION
RSG’s inspection procedures
include detailed review and analysis of shop drawings, engineering
drawings, and approval of contractor’s pay requisition. We
advise the contractor of the various change orders and field revision
as necessary per project or Client requirements.
We prepare detailed plan reports, final approved plans, specifications
and construction estimates. Our staff provides detailed progress
reports throughout the life of the project.
|
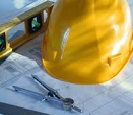
|
QUALITY
ASSURANCE
In accordance with the
Client approved QC/QA plan, inspect, monitor, and document the
activities of the contractor, subcontractors, and suppliers to ensure
compliance with the requirements of contract documents.
- Review the contractor’s
quality control plan Meet with contractor to define and interface
Client quality program to contractors program.
- Define quality roles and staff
assignments as necessary.
- Establish processes to allow for
proper implementation of the quality plan.
- Develop written procedures to
implement the approved Client QC/QA plan in the field. Generate a
comprehensive QC/QA matrix for each of the specifications.
- Implement the approved project QA
procedures.
|
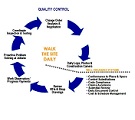
|
CLAIMS
AVOIDANCE
The RSG team’s approach to
claims avoidance begins with preventing claims by assuring the
development of properly conceived contractual terms that clearly assign
risks to the parties best suited to deal with them, and complete,
coordinated design drawings and specifications detailing the technical
and operational requirements of the Contract Documents. Claims
avoidance actions during construction should entail:
- Get an accurate baseline schedule
and updates. The baseline schedule will help discourage submittal of
time-related claims by accurately identifying critical work items and
quantifying resource requirements planned for each item of work.
- Carefully monitor and rapidly
respond to correspondence, submittals, RFIs, and RFSs to identify
potential problems and minimize the Contractor’s opportunities to
claim delays.
- Pro-actively manage the
procurement, fabrication, quality assurance and delivery of Client
pre-purchased equipment and material.
- Maintain open communication and an
open mind when listening to the Contractor’s ideas or complaints
and work with the Contractor to solve problems early.
- Participate proactively in
“partnering” with the Contractor during the term of the
contract.
- Maintain a “tough but
fair” attitude with the Contractor to assure that the Client is
not taken advantage of and the Contractor is treated fairly,
particularly on change orders issues.
- Be as knowledgeable as the
Contractor as to the “history” of the project and maintain
thorough and comprehensive records.
- Maintain constant job
“presence” at the worksite and in the offices to allow
constant observation of the work and quick response to problems.
|
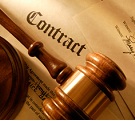
|
CHANGE MANAGEMENT
The Construction Manager is
responsible for managing the change management process in conformance
with the requirements in the Contract Documents, leading the
negotiation of cost and/or time impacts, and providing recommendations
for the disposition of Change Requests. The Office/Field Engineer
assists the Project Construction Manager in managing the change
process, maintains all change request files, and records of
negotiations and maintains the Change Log. The Project engineer
will support the preparation of owner requested changes and review of
all technical Change Requests.
|
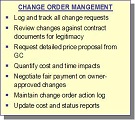
|
NEGOTIATION
of CHANGES
The RSG team’s approach to
change request negotiations is to negotiate fairly and openly using the
Contract Documents as the basis of any settlement. The goal should be
to answer the change request within one payment cycle. The
construction Contract Documents will include requirements for the
necessary documentation that must be used and accompany all change
requests. |
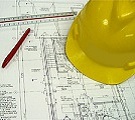
|
|
|
|
|
|